
ROOF PA100 REPAIRS & PROTECTS A FAILING EPDM COMMERCIAL ROOF
- LOCATION: BRONX, NYC
- DATE APPLIED:
- SUBSTRATE: EPDM
- PRODUCT USED: WBE PRIMER & ROOF PA100
- APPLICATION METHOD: BRUSH & SPIKED ROLLER
- SITE DESCRIPTION: COMMERCIAL 10,000 SQFT ROOF
THE CHALLENGE
A commercial building in the Bronx, constructed in 1980, faced the common dilemma of an aging failing EPDM roof causing leaks. Traditional repair methods, often inadequate for older EPDM membranes, proved insufficient to address the underlying issues.
Constant exposure to UV radiation, thermal fluctuations, and mechanical stress induces fatigue, leading to cracks, punctures, and compromised seams in worn EPDM. Aging adhesive bonds at seams and penetrations also lose their effectiveness over time, creating entry points for water infiltration and leaks. Flat or low-slope configurations can lead to water accumulation, accelerating material degradation and promoting leak development.
These combined challenges render traditional repair methods like patching ineffective in the long term. Patching merely addresses isolated symptoms without tackling the underlying root causes. Therefore, a multifaceted solution capable of providing a seamless, durable barrier against water and weather becomes crucial for successful rehabilitation.
THE SOLUTION
The Armus Roof PA100 system, with its two-phase approach, addressed the specific needs of the Bronx building's aging EPDM.
Water-borne Epoxy Primer: This low-VOC primer penetrates and seals minor imperfections and cracks, forming a robust bond with the substrate. Its application across the entire surface and critical points like penetrations creates a stable foundation for the topcoat.
Roof PA100 Topcoat: This highly elastomeric polyurea coating exhibits exceptional water repellency, forming a seamless, monolithic barrier against leaks. Its high elongation at break (450%) allows for exceptional adaptability to temperature variations, minimizing the risk of cracking or tearing. Additionally, its cool roof technology reflects solar heat, contributing to energy cost reductions.
IMPLEMENTATION
Following a thorough cleaning and debris removal, the Water-borne Epoxy Primer was applied via roller, ensuring complete coverage and optimal adhesion. After proper curing, the Roof PA100 topcoat was applied, forming a uniform, watertight seal across the entire surface.
Immediate results were evident. Leaks were effectively eliminated, restoring the roof's integrity and providing protection against water ingress. The cool roof technology further delivered tangible benefits by reducing the building's energy consumption.
POST-APPLICATION RESULTS & evaluation
This case study exemplifies the efficacy of the Armus Roof PA100 system in revitalizing aging EPDM roofs. By addressing the inherent challenges associated with traditional repair methods, the Roof PA100 system offers a long-term, cost-effective solution that extends the lifespan, enhances energy efficiency, and restores structural integrity.
The recent use of Armus Roof PA100 as a repair coating at this site provided an opportunity to demonstrate and confirm some of the fundamental concepts with simple field data. Non-contact temperature measurements were made with a laser-guided infrared thermometer. Air temperatures were measured conventionally.
One half of the existing roof had already been repaired. This meant that areas of both the aged EPDM and the new Armus Roof PA100 surface were accessible for study. At three hours after sunrise with air temperature measured at 88°F, the temperature of the EPDM surface was already at an average of 148.6°F. The portion of the roof surface coated with Armus Roof PA100 was, at the same time, at 98.9 degrees. The building was in continuous use during the roof repair project, with the HVAC temperature set at 71°F.
This successful application demonstrates the system's versatility and effectiveness as a reliable partner in safeguarding roofs against the effects of time and weather, while also demonstrating Roof PA100’s energy saving ability through its highly reflective properties.
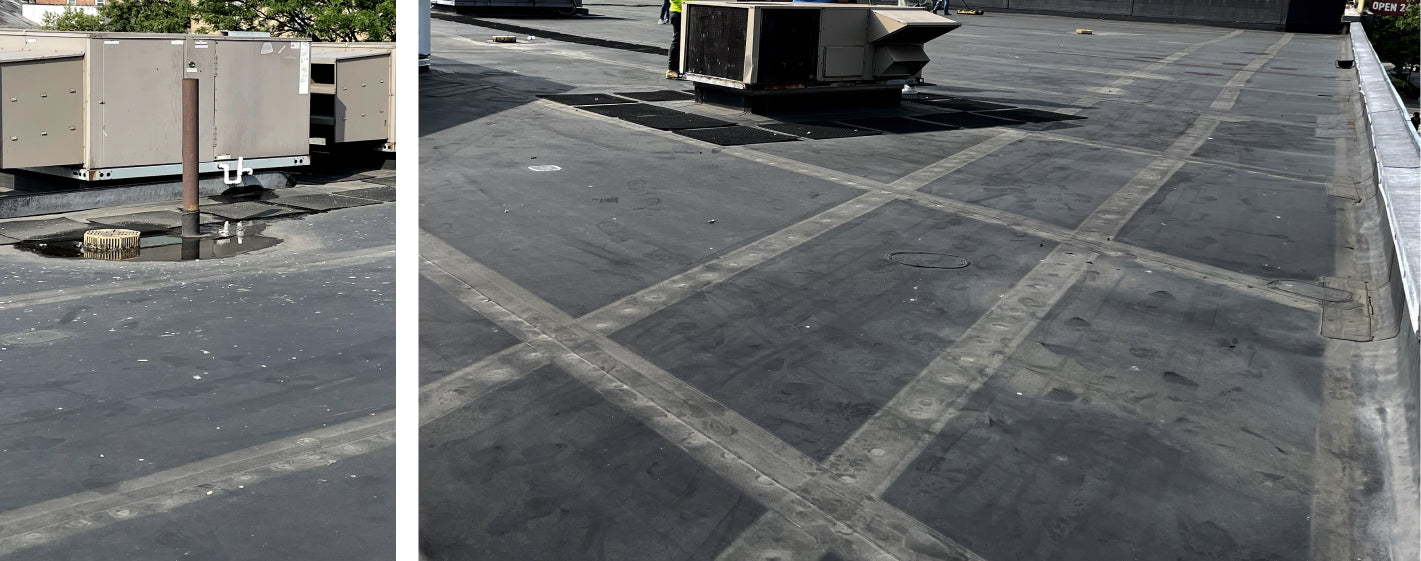
project gallery
Pre-cleaning site visit. Existing worn EPDM visible with ponding water and surface damage visible.

After WBE Primer application & curing (seen as transparent glossy sheen on EPDM). Roof PA100 topcoat applied at penetration points & flashing.
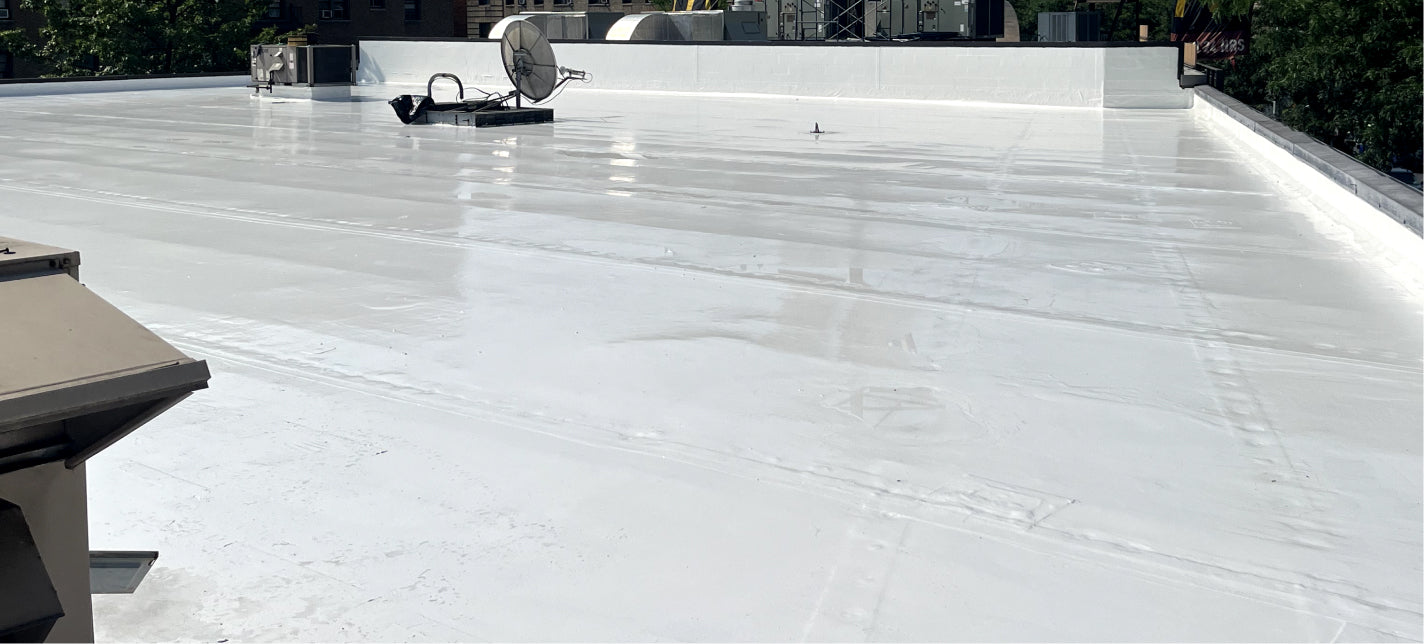
Roof PA100 topcoat. Post-application.
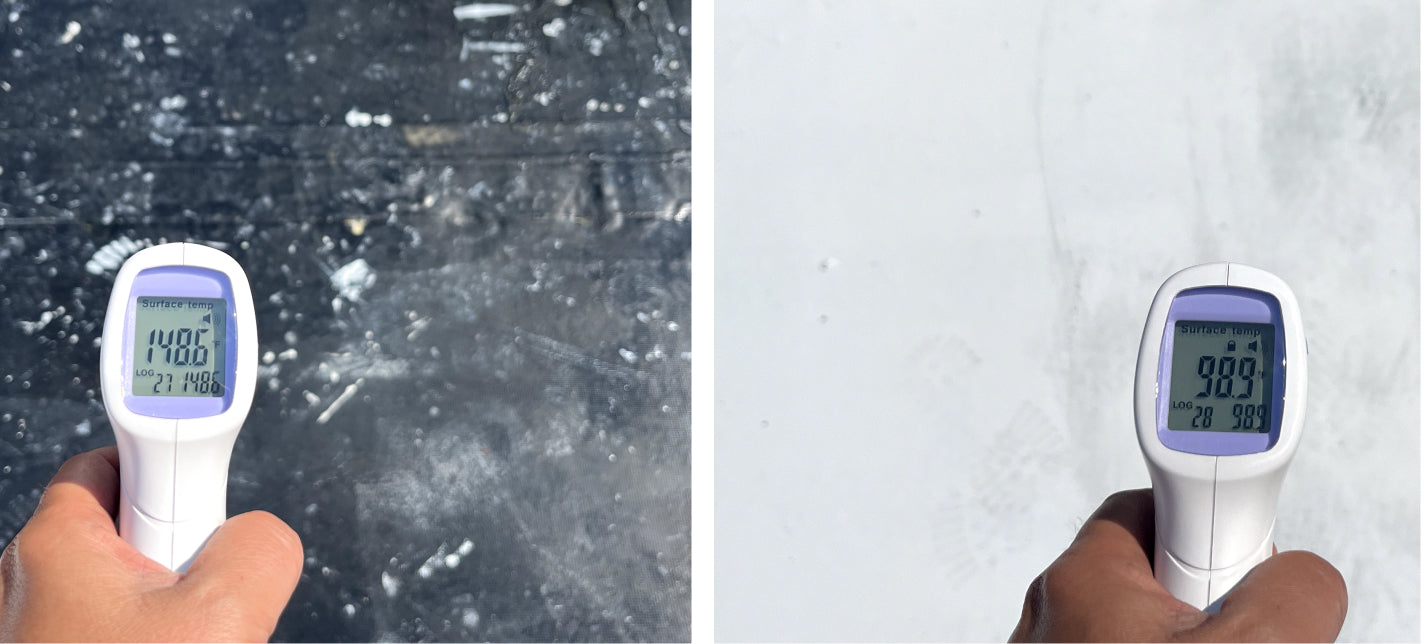
On the same half-coated EPDM roof, Roof PA100 topcoat exhibits high reflectivity with lower surface temperature.
Video

WBE Primer
A TWO-PART WATER-BORNE EPOXY PRIMER THAT CREATES A WATERPROOF BARRIER AND PROVIDES HIGH ABRASION RESISTANCE.
Use with Armus Roof PA100 topcoat.


Roof PA100
A two-part polyaspartic roofing repair topcoat that creates a waterproof barrier, blocks heat transfer and provides thermal insulation.
Use with Armus water-borne epoxy primer.
